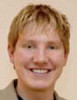
Dipl.-Ing. Sebastian Theiß
Dipl.-Ing. Sebastian Theiß studierte von 2001 bis 2007 Elektrotechnik und Informationstechnik mit der Vertiefungsrichtung Plasmatechnik an der Ruhr-Universität, Bochum. Seit 2007 ist er Wissenschaftlicher Assistent am Institut für Oberflächentechnik im Maschinenbau im Bereich der PVD-Technologie (Werkzeuge) an der RWTH Aachen University.