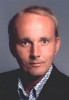
Prof. Dr.-Ing. Markus Feldmann
Professor Dr.-Ing. Markus Feldmann, geb. 20. Mai 1966 in Siegen, schloss sein Studium des Bauingenie...Professor Dr.-Ing. Markus Feldmann, geb. 20. Mai 1966 in Siegen, schloss sein Studium des Bauingenieurwesens an der RWTH Aachen University 1991 als Dipl.-Ing. ab. Nach kurzer Zeit in der Industrie arbeitete er anschließend als wissenschaftlicher Mitarbeiter am Lehrstuhl für Stahlbau, wo er 1994 zum Dr.-Ing. promovierte. Nach weiterer Beschäftigung in Wissenschaft und Industrie ist er seit 1999 geschäftsführender Gesellschafter im jetzigen Ingenieurbüro Fa. Feldmann + Weynand GmbH. 2001 folgte er zunächst dem Ruf zum Universitätsprofessor für Stahlbau an die TU Kaiserslautern, bevor er 2004 zum Universitätsprofessor des Lehrstuhls für Stahlbau und Leichtmetallbau der RWTH Aachen University und Leiter des Institutes für Stahlbau berufen wurde.