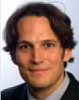
Dipl.-Ing. Andreas Roesner
Dipl.-Ing. Andreas Roesner hat den Diplomstudiengang Maschinenbau mit Vertiefungsrichtung Kunststofftechnik an der RWTH Aachen 2007 erfolgreich abgeschlossen. Nach langjähriger Tätigkeit als studentische Hilfskraft am Fraunhofer Institut für Lasertechnik (Aachen) arbeitet er dort seit Januar 2008 als wissenschaftlicher Mitarbeiter in der Abteilung Mikrotechnik. Seine Arbeitsgebiete sind Kunststoffschweißen und Metall-Kunststoff-Fügen.